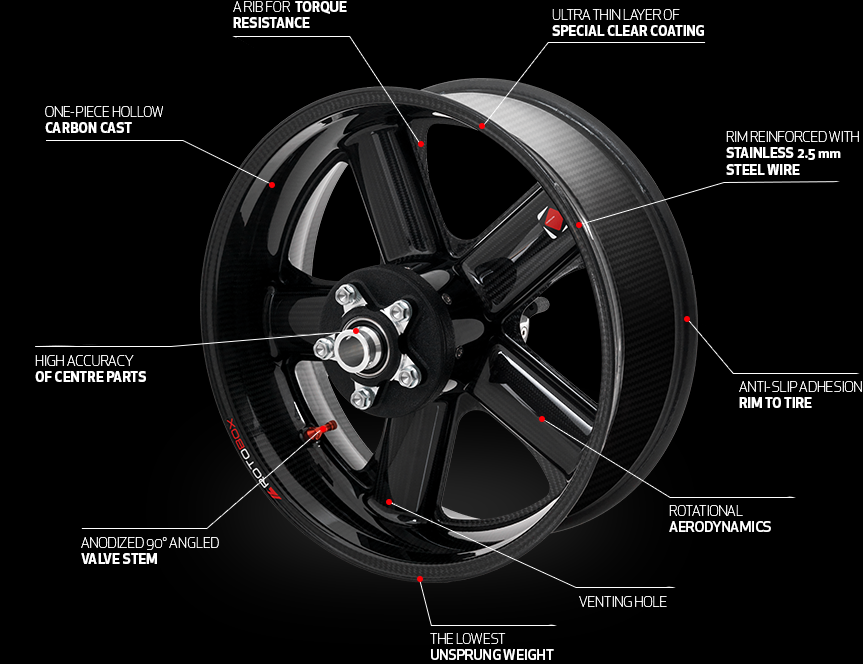
HOW TO MAKE THE LIGHTEST AND STRONGEST WHEEL IN THE WORLD?
Probably not everyone asks themselves this question. It is also very probable that not everyone can make such a product.
In fact that is exactly what they told to Gregor Bizjak when he decided to take on the challenge and succeed. This was in year 2005 and now it is made and functional. In order to design and manufacture the lightest wheel you need to know all there is to know about motorcycle racing. And in order to make something no one has ever succeeded, you must know that impossible is just a word.
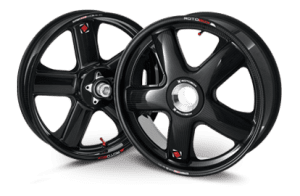
Rotobox wheels the best technology for your money
PRODUCTION OF THE CENTRE PARTS
The centre part of the wheel includes hubs, spacers, sprocket carrier and disc carrier, which are made of aluminium alloy 7075 T6 intended for high pressure. All parts are CNC machined at accuracy of  ±0.02 mm for each bike model specifically and protected with highly resistant electrostatic powder coating. The hubs are joined to the carbon cast with specific glue and M6 screws. The wheels are finally assembled at accuracy of  ±0.01 mm.
.
PRODUCING ONE-PIECE HOLLOW CARBON CAST
The process of producing one-piece hollow carbon “monocoque” cast is an adaptation to the high pressure Resin Transfer Molding technology with highly precised aluminium tools CNC made specifically for a wheel design. The carbon fiber laminate includes 6 different types of carbon fabric, which are CNC tailored and hand placed into the tools. The carbon fiber textile and epoxy resin used are of the highest quality initially used for the aviation industry, produced in Europe.
The shape, structure and dimensions of each wheel are defined by highly precised aluminium tool CNC made specifically for a wheel design, which enables continuity and replicability of the carbon casts.
In defense of radiation we protect the carbon casts with UV-resistant layer of clear coat. We are extremely proud of the quality of one-piece carbon casts, the continuity of the procedure and subsequent safety, which we ensure with the best technology.
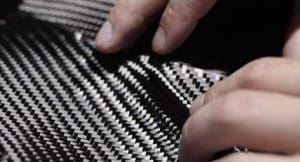
Rotobox Carbon casting
THE MAN BEHIND THE PERFECT WHEEL
Gregor Bizjak has worked as a research and development engineer since 1997 and obtained experiences with production management, CAD designing, CAM programming, reverse engineering and development of tools.
As a racing motorcyclist Gregor thought of the idea to develope and produce a carbon fiber wheel for motorbike with revolutionary design and technical perfection in order to achieve maximum racing performance. This design demanded that Gregor come up with a novel way of producing a one-piece hollow carbon construction, something much more complex than what has been allowed previously. Gregor has truly reinvented the wheel.
INTELLECTUAL PROPERTY AND PATENTS
The ROTOBOX wheel is patented in Slovenia with register number 22709. The ROTOBOX wheel has approven international patent application with register number PCT/SI2008/000069 and patent is beeing registered in different countries all over the world
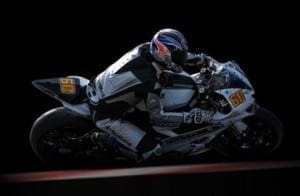
The man behind the petented Rotobox Carbom Fibre wheel
TESTING LABORATORY
The ROTOBOX wheels correspond to the safety standard JASO T203-85 for JWL dotE, which requires testing at four different fatiques. Because safety is the most important feature the company has its own rigorous laboratory for testing Cornering, Radial, Torsional fatigue and Drop test.
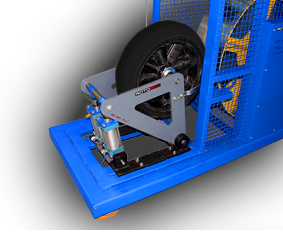
Rotobox RADIAL FATIQUE TEST The wheel is exposed to rotational forces.
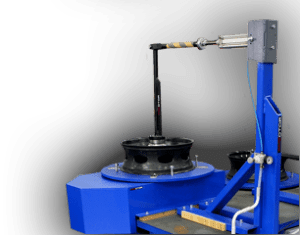
Rotobox CORNERING FATIQUE TEST The wheel is exposed to assymetrical torque.
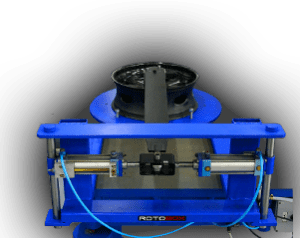
Rotobox TORSIONAL FATIQUE TEST The wheel is exposed to torsic torque.
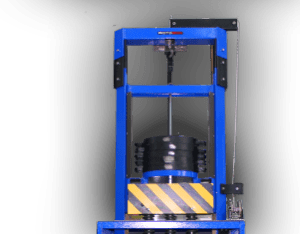
Rotobox IMPACT TEST The load is dropped on the wheel.